Enhancing Welding Processes Using Machine Learning-Based Defect Analysis

Background
Welding is a critical process in industries such as construction, automotive, aerospace, and shipbuilding, but defects like porosity, spatter, arc strikes, and improper cross-sectional profiles often compromise quality and structural integrity. Detecting and addressing these defects is labor-intensive and costly when done manually, highlighting the need for automated solutions.
Objective
This project aims to develop an AI algorithm capable of detecting and analyzing welding defects in real time using data from cameras and 2D laser scanners. The ultimate goal is to enhance the quality, efficiency, and safety of welding processes across industries.
Key goals include:
- Accurate detection of defects, including porosity, spatter, arc strikes, and incorrect cross-sectional profiles.
- Integration of AI models with camera and laser scanner data.
- Training on diverse datasets to handle varied scenarios and conditions.
- Optimization to minimize false positives and negatives.
- Validation through testing in real-world welding applications.
Approach
To tackle the problem, the project leveraged AI and machine learning techniques, focusing on defect detection using camera images and laser-scanned cross-sectional profiles. The methodology included:
- Data Collection:
- Capturing weld images and profiles with 2D laser scanners.
- Compiling a large dataset of welding scenarios and defect types.
- Model Development:
- Creating an AI algorithm for defect classification and real-time detection.
- Using advanced machine learning models to improve detection accuracy.
- Training and Optimization:
- Training the AI model on diverse datasets to handle various defect scenarios.
- Fine-tuning to reduce false positives and negatives.
- Integration and Testing:
- Integrating the AI algorithm with welding inspection systems.
- Testing in real-world environments to ensure reliability and effectiveness.
Results and Impact
The AI algorithm successfully identified a variety of welding defects in real-time, significantly reducing manual inspection time and costs. Key results include:
- Improved weld quality and strength by enabling timely defect detection and correction.
- Enhanced productivity by automating defect detection, minimizing downtime.
- Cost savings for manufacturers through reduced rework and material wastage.
- Strengthened safety and reliability of welded products, reducing failure risks.
This innovation positions industries to meet higher quality standards while achieving operational efficiency.
Future Implications
The AI-driven welding defect detection system could revolutionize quality assurance in manufacturing. Its potential applications span:
- Construction: Improving the safety of structural welds in buildings and infrastructure.
- Automotive: Ensuring defect-free welding in vehicle components for enhanced safety.
- Aerospace: Maintaining stringent quality standards in critical aircraft parts.
- Shipbuilding: Preventing failures in ship hulls and structural components.
Future research could expand the solution to detect more complex defects and adapt to emerging welding technologies, ensuring continued advancement in automated quality control systems.
This challenge is hosted with our friends at



Become an Omdena Collaborator
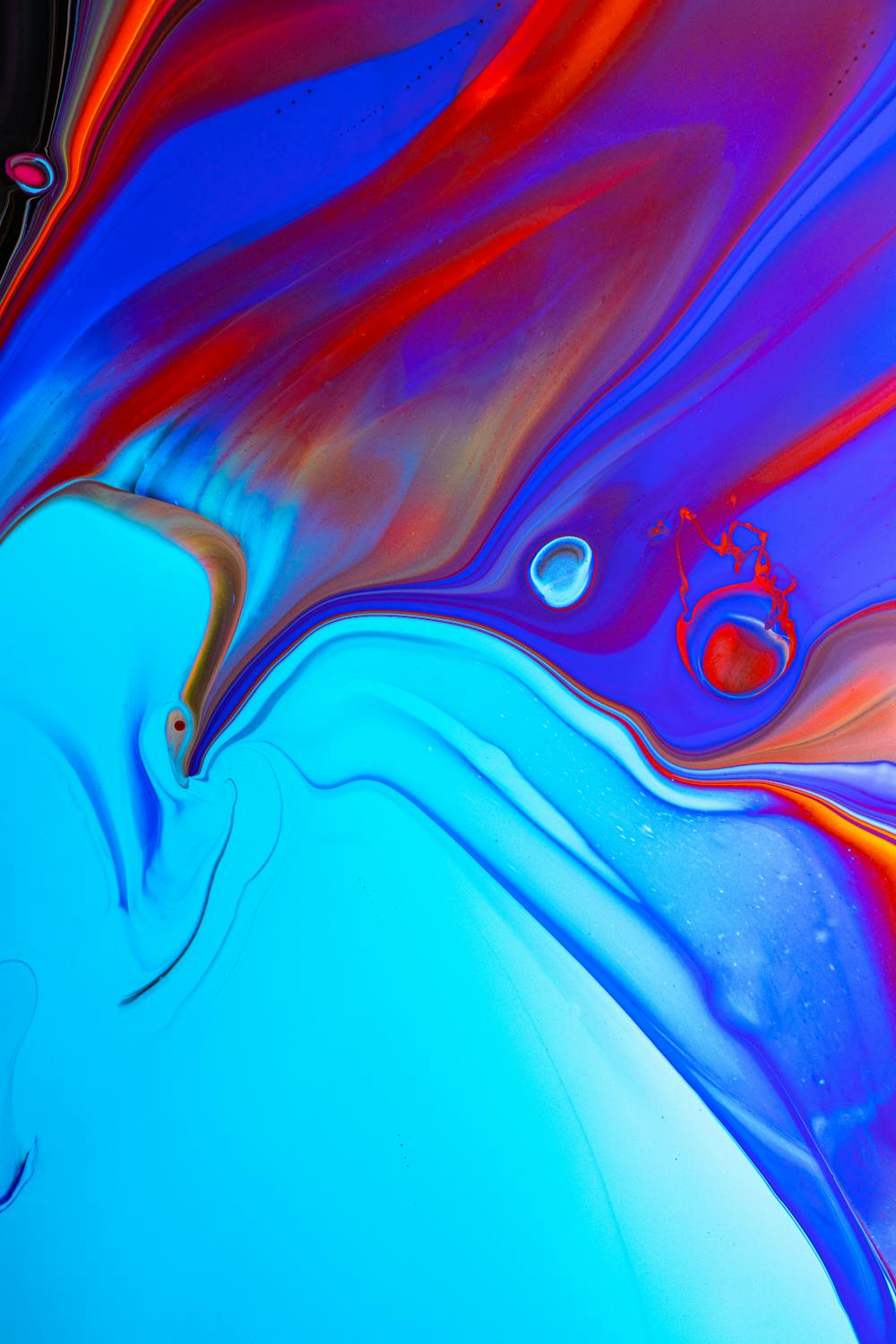